New 3D printers could transform space construction
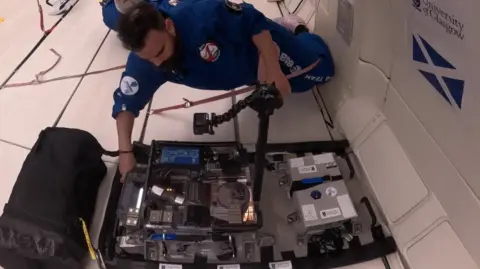
On-board manufacturing for spacecraft is one small step closer with the development of new 3D printing technology in zero gravity.
Dr Gilles Bailet, from the University of Glasgow's James Watt School of Engineering, has been awarded a patent for a system to carry out construction on-demand during a space flight.
He hopes the technology - which has been tested on a zero-gravity research aeroplane - could make space exploration more sustainable and reduce space debris.
Dr Bailet said his invention, using granular materials, could support plans to manufacture in space novel equipment not possible on Earth.
"As the cost of sending things into space is decreasing, we are seeing more and more things sent into space and this is not sustainable," Dr Bailet said.
"Our idea is to be able to manufacture things directly in space using 3D printing and in doing so we open the door to recycling in space and to have a full circular economy."
The International Space Station (ISS) was sent its first 3D printer in 2014 and research on manufacturing parts away from the Earth's gravitational pull has continued since, both here and in orbit.
Dr Bailet's prototype 3D printer uses a granular material instead of the filaments used on Earth.
Despite the challenges of microgravity and the vacuum of space, the materials can be drawn from a feedstock tank and delivered to the printer's nozzle faster than other methods.
It was tested in November as part the 85th European Space Agency parabolic flight campaign with Novespace in Bordeaux, France.
The team took its test kit on three flights, giving them more than 90 brief periods of weightlessness at the apex of rollercoaster-like sharp ascents followed by rapid descents.
"Seeing the technology actually working perfectly as I designed it was really breathtaking, a lot of emotions," he said, referring to the tests on the zero gravity aircraft - known as the vomit-comet for its rollercoaster-type flight that provides 22 seconds of microgravity every time it lurches over a peak.
"Now we know that our technology is working in a space environment and we'll be able to do the first demonstration in space in the next milestone of our technology development."

Dr Bailet and his colleagues are also exploring methods of embedding electronics into the materials as part of the printing process.
"Currently, everything that goes into Earth's orbit is built on the surface and sent into space on rockets," Dr Bailet said.
"They have tightly limited mass and volumes and can shake themselves to pieces during launch when mechanical constraints are breached, destroying expensive cargo in the process."
He added that products made on Earth can be "less robust in the vacuum of space", and 3D printing has only been successfully done in the pressurised modules of the ISS so far.
While Dr Bailet's project is currently working on building parts to enhance spacecraft, such as radiators and antennae, it is hoped that equipment could eventually be built in space.
These could include solar reflectors to generate zero-carbon power for transmission back to Earth, improved communication antennae, or drug research stations that can create purer, more effective pharmaceuticals.
"Crystals grown in space are often larger and more well-ordered than those made on Earth, so orbital chemical factories could produce new or improved drugs for delivery back to the surface," he added.
Dr Bailet and his team are now looking for funding to help support the first in-space demonstration of their technology.